Interview with Andreas Reichinger, Senior Research Engineer at VRVis Center for Virtual Reality and Visualization Research GmbH, Austria's leading research institution for application-oriented research in the field of visual computing
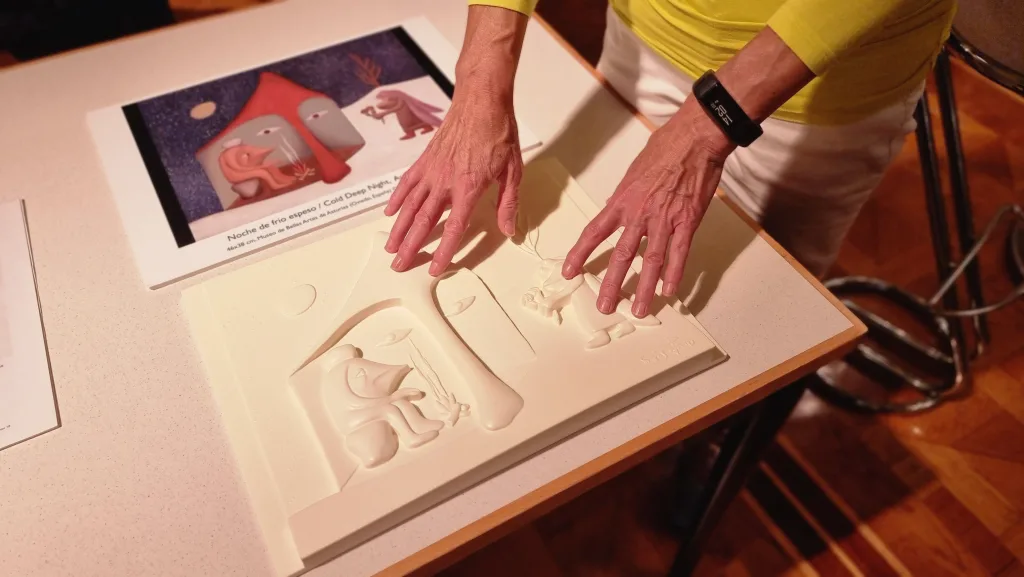
Museum Guide: We are standing here in your research office, in front of us is a series of reliefs of varying gradations and qualities that can be used to explain your research work. Can you describe the complex development process behind it?
Andreas Reichinger: In 2010, we were commissioned by the Kunsthistorisches Museum to work on converting works of art into tactile forms in order to make it easier for people with visual impairments to access art. The status quo at the time was swelling prints, where a tactile effect was created on special paper by heating it. Braille printers were also used. These were very simple and cheap makeshift devices, but they were far from being able to allow the many dimensions of a work of art to be felt.
We were initially concerned with the question of how to make the sense of depth that artists create in their paintings possible in a printed relief image? Using Raphael's "Madonna in the Green", I then wrote software that can be used to segment the individual areas of a painting in order to assign them different levels of depth. This is not trivial, because if you look at the arms of the Madonna, for example, as she holds the child, then I have to take several levels and transitions into account here alone. The three-dimensionality created in the original through light and dark effects as well as patterns and shading are extracted in the program using filters that are modeled on the perception of the human eye and are applied as surface variations in the relief. Important areas such as faces, bodies and geometric objects are digitally remodeled and integrated into the overall image.
Museum Guide: What process and material is used to create the relief?
Andreas Reichinger: The depth image created on the computer is produced using a computer-controlled CNC milling machine. This has the advantage over 3D printers of delivering higher quality results, and I have a free choice of materials. This is even more important at the moment in terms of hygiene and disinfection. In addition, milling of this quality and size is still cheaper and faster. If requested, we can also make a negative impression in silicone, which can then be cast in plastic and reproduced many times, which is very popular for group tours.
Museum Guide: What is innovative about your research work, what distinguishes your relief images from manually made reliefs?
Andreas Reichinger: The inspiration for our relief images comes from sculpture. For example, from the tradition of the Italian "Museo Tattile", where paintings or architectural models are reproduced for blind people. A British artist recreates relief images from clay, others carve them from soapstone. The craftsmanship and personal interpretations then determine the result and the quality. The computer, on the other hand, enables exact reproduction and reproducible results that can also be corrected at any time.
Museum Guide: What is the added value of these reliefs for the museum?
Andreas Reichinger: The added value goes far beyond the educational work for people with visual impairments. From the beginning, my aim was to be able to produce relief images on the computer that are interesting and informative for everyone, not just for people with visual impairments. When the relief of the Raphael Madonna was exhibited for the first time in the Kunsthistorisches Museum, right next to the original painting, almost all visitors approached the relief with interest and spent longer than usual looking at the painting. The relief enables a different, additional approach to the work of art; it opens up new perspectives.
Museum Guide: How long does it take to develop a relief?
Andreas Reichinger: Each picture presents us with its own new challenges, and the development time can vary accordingly. In this respect, each relief is created manually, albeit on the computer. For the very first relief, the Raphael relief, we are talking about months; it was done as part of a research project. At the moment we are at 1 to 2 weeks. First I write a "treatment" - how do I see the picture, how does the client see it? This requires in-depth analysis and often discussions. Because the description of the picture has a significant influence on the quality of the result. Then I give the description to blind test subjects. Based on the feedback, a first rough draft is created on the computer, then comes the detailed draft. The final milling takes between 12 and 24 hours.
Museum Guide: You now produce for many museums.
Andreas Reichinger: We are often partners in EU research projects, but we also work as direct contractors for art and cultural institutions. In addition to the Kunsthistorisches Museum, our reference museums include the Technical Museum, the Belvedere, the Dommuseum Wien and the Graz Museum Schlossberg. Our reliefs are also exhibited throughout Europe, for example in the Museo de Bellas Artes de Asturias, the Victoria & Albert Museum, the Museo Thyssen-Bornemisza, the Wallace Collection, the Museo Lazaro Galdiano, the Berlinische Galerie and the Haus der Bayerischen Geschichte in Regensburg.
Museum Guide: What is the feedback from visitors?
Andreas Reichinger: One encounter that particularly touched me was a lady who thanked us with tears in her eyes. She had always been an art lover before she went blind and thought that the door to art was now closed for her. Through our work, this door has opened again. We have been awarded several prizes for our research contribution to more inclusion and our inclusive art solutions, for example the Heritage in Motion Award 2020 and the WSA Austria Award 2020.
Museum Guide: What is the next step, the next development?
Andreas Reichinger: Another area of research is tactile photography, where we not only enable visually impaired people to take photos themselves in workshops, but also produce relief photos, including a new type of relief printer. Our main focus, however, is on new communication channels, particularly in the spirit of "Design for all": In a three-year EU-funded research project, we have developed a tactile, interactive multimedia guide that not only serves people with visual impairments, but also takes a wide variety of needs into account. On a screen with a built-in camera that detects the touch of a relief, you can choose between a variety of information channels and perception options: projections and animations in color, representations as sounds, audio explanations, descriptions in sign language and in easy language, background information and much more - in other words, a guide for everyone, including people without disabilities. That is important to me! Everyone and their needs should and can be taken into account. The focus is not on the type of disability, but on the different needs.
Contact: VRVis Center for Virtual Reality and Visualization Research GmbH Donau-City-Str. 11, 1220 Vienna office@vrvis.at +43 (1) 908 98 92